In today’s dynamic construction landscape, the pressure to deliver high-quality, cost-effective, and sustainable buildings has never been greater. Amid these demands, Value Engineering (VE) has emerged as a powerful methodology that supports decision-making beyond conventional cost-cutting. When strategically applied, VE offers a structured, function-oriented approach to achieving optimal project outcomes without compromising on quality, performance, or aesthetics.
Understanding Value Engineering
Value Engineering is defined as a systematic approach aimed at analysing the functions of systems, components, and processes to identify cost-saving opportunities that do not reduce value. Instead, VE focuses on improving the function-to-cost ratio by considering various alternatives for design, materials, and construction methodologies. This includes evaluating lifecycle costs, performance durability, operational efficiency, and visual appeal.
Contrary to common misconceptions, VE is not a tool for simply reducing costs. Rather, it ensures that every project element performs effectively at the lowest possible cost, delivering maximum value throughout the building’s lifecycle.
Value = Function / Resources
The Strategic Importance of Value Engineering in Construction
The application of VE in construction delivers a range of critical benefits:
- Cost Optimisation: Identifies and eliminates unnecessary expenditures while maintaining or enhancing function.
- Enhanced Efficiency: Improves project schedules and resource allocation by streamlining processes and eliminating redundancies.
- Sustainable Outcomes: Considers environmental impact and long-term maintenance costs, promoting the use of sustainable materials and techniques.
- Stakeholder Alignment: Helps project teams meet or exceed client expectations by ensuring performance, cost-efficiency, and timely delivery.
Core Phases of Value Engineering
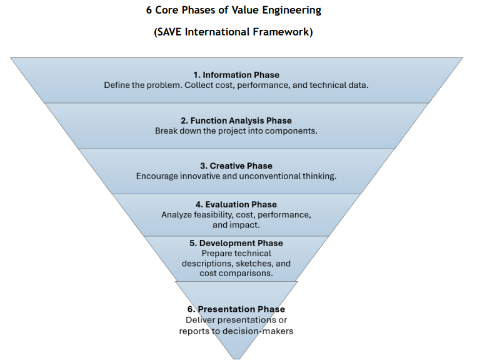
According to the SAVE International framework, VE follows a six-phase methodology:
- Information – Gathering relevant project data and understanding client objectives.
- Function Analysis – Defining the primary and secondary functions of each element.
- Creative – Generating alternative solutions.
- Evaluation – Analysing alternatives for feasibility, cost, and impact.
- Development – Preparing VE proposals with technical justification and cost-benefit analysis.
- Presentation – Communicating the recommendations to stakeholders for approval and implementation.
Industry research indicates that VE can deliver average savings of 10–30% per project, with returns on investment as high as 20:1 in some cases.
Key Approaches to Value Engineering
1. Material Substitution
Selecting alternative materials that meet performance requirements at a lower cost. For example, replacing traditional plaster with gypsum boards in arid climates can reduce both material costs and environmental impact.
2. Process Optimisation
Adopting techniques such as prefabrication to reduce construction timelines, improve quality control, and minimise on-site labour.
3. Design Simplification
Reducing unnecessary complexity through modular and standardised designs to lower material usage and enhance constructability.
Application Across Project Phases
While traditionally conducted during the design phase, VE can be equally effective during the construction phase. Early-stage implementation enables alignment with client goals and value delivery from the outset. However, even during execution, VE proposals—when carefully evaluated—can result in meaningful improvements. These proposals must be reviewed thoroughly to ensure they do not disrupt timelines or compromise the design intent.
ECC Group’s Approach to Value Engineering
ECC Group has institutionalised Value Engineering as a core pillar of its project delivery strategy. By integrating VE with Lean construction principles and BIM (Building Information Modelling), ECC ensures that each project is optimised for cost, time, performance, and sustainability.
VE has been extensively applied in several high-profile ECC projects such as The Peninsula in Business Bay, the Bridge District, and developments in Dubai Creek. These projects exemplify how structured design optimisation can yield tangible improvements without sacrificing architectural quality.
Practical VE Applications from ECC Projects
- Use of spray plaster and paint finish instead of traditional cement-sand plaster for ceilings
- Adoption of prefabricated bathroom pods to streamline installation
- Implementation of Fortis Panels instead of block and plaster
- Use of void formers instead of conventional lightweight filling materials
Value Engineering remains a critical tool in the modern construction toolkit. By focusing on long-term performance, cost efficiency, and stakeholder satisfaction, VE supports the delivery of smarter, leaner, and more sustainable buildings. ECC Group’s continued commitment to this methodology demonstrates its role as a forward-thinking contractor dedicated to excellence across every stage of construction.