ECC Group’s pursuit of operational excellence is anchored in the principles of Lean Construction—maximising value, eliminating waste, and driving continuous improvement across all functions. Among the tools employed to support this initiative, Value Stream Mapping (VSM) has emerged as a key enabler of process optimisation.
Understanding Value Stream Mapping (VSM)
Value Stream Mapping is a Lean methodology designed to visualise each step within a process, from inception to completion. By highlighting both value-adding and non-value-adding activities, VSM enables the identification of inefficiencies, bottlenecks, and delays, allowing for informed decision-making and targeted improvements.
Application of VSM at ECC Group
ECC Group adopts a structured approach to VSM implementation:
- Current State Mapping: Comprehensive documentation of all activities, delays, and handoffs
- Bottleneck Identification: Analysis of points where workflows are disrupted or delayed
- Takt Time Calculation: Takt Time = Available Time / Customer Demand
- Used to ensure production aligns with demand expectations
- Resource Balancing: Optimisation of manpower and workload distribution
- Future State Design: Development of streamlined, flow-oriented process models
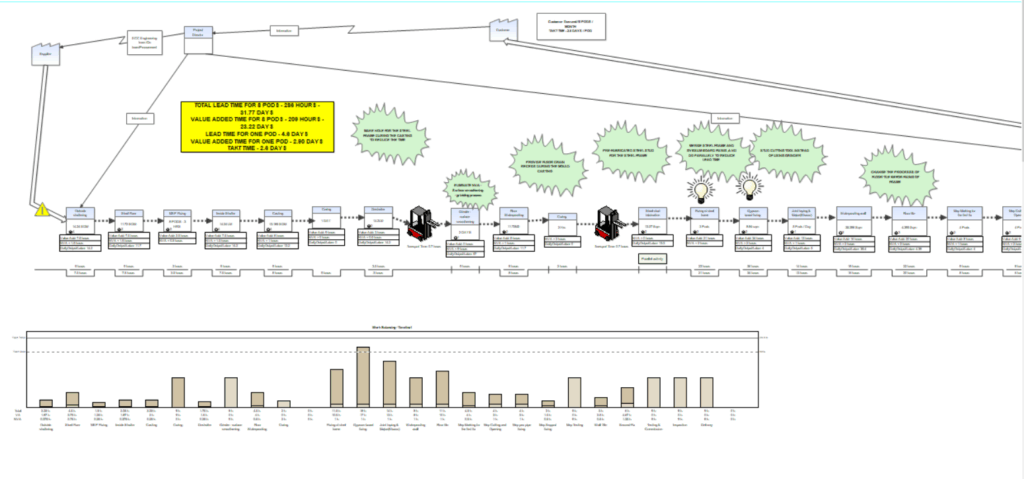
Case Study: Implementation in the Bathroom Pods Division
The Bathroom Pods Division recently underwent a comprehensive VSM exercise aimed at reducing production lead time and enhancing overall process efficiency.
Current State Assessment
- Lead Time: 14 days per batch
- Identified Bottlenecks:
- Wall tile installation
- Floor tile installation
- Grouting of wall tiles
- Takt Time: 1 pod every 5.49 hours (based on 45 pods in 26 days)
- Primary Constraint: Imbalanced workload resulting in production delays
Strategic Objectives and Interventions
Based on the current state assessment, the following objectives were established:
- Target Cycle Time: Reduction to 12 days per batch
- Balanced Workstations: Introduction of equitable task allocation
- Takt Time Alignment: Synchronisation of production flow with calculated takt time
- Improved Resource Utilisation: Enhanced sequencing and manpower deployment
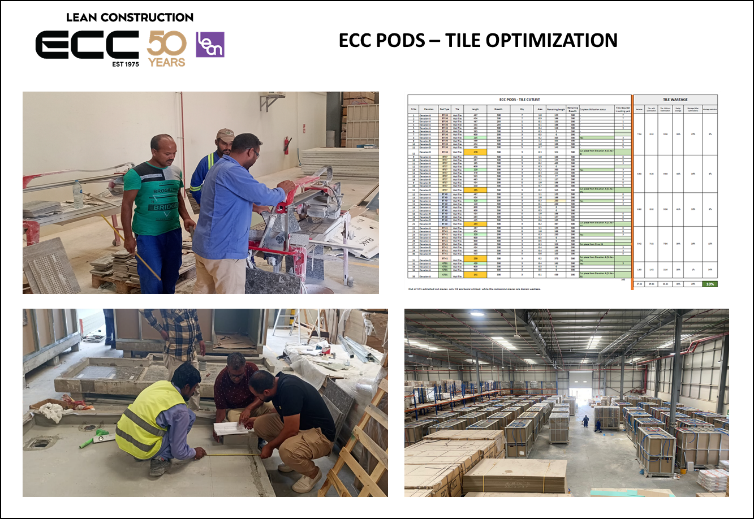
Key Improvements Implemented
- Parallel Wall Stud Fabrication: Mitigated start-up delays
- Optimised Tile Installation Sequence: Floor tiles installed prior to wall tiles to improve workflow
- Twelve Lean Interventions: Each aimed at achieving a minimum of 10% time savings per task
- Workload Redistribution: Streamlined tasks across all stations
- Centralised Tile Cutting Area: Improved speed and accuracy
- Refined Casting Method: Transitioned from upside-down casting to a more efficient technique
Further Enhancements Under Review
With inputs from Engineer Ayman Ezzeldeen Abdalla and Engineer Bassam Shaath, the following enhancements are currently under evaluation for additional efficiency gains and cost optimisation:
- Integration of steel-based concrete
- Use of Marmox boards for ceiling applications
- Implementation of steel trolleys for production lines
- Deployment of automated stud fabrication machinery
- Adoption of PSB® (Palm Strand Board) panels for walls and floors
In addition to technical advancements, the VSM initiative fostered enhanced cross-functional collaboration. Teams across all levels demonstrated a shared commitment to performance improvement, reinforcing a culture of continuous development.
Outcomes Achieved
- 14.2% reduction in overall lead time
- 25.6% decrease in tile material wastage
- 16% improvement in quality approval rates for bathroom pods
The successful application of Value Stream Mapping within ECC Group’s Bathroom Pods Division underscores the organisation’s dedication to Lean practices and structured process improvement. Through data-driven analysis, innovative process design, and cohesive execution, ECC Group continues to set benchmarks in construction efficiency and quality.